Polishing
My approach when polishing a sword is to restore/finish a blade is by removing the least amount of material as possible while maintaining the shape the smith intended. Bring out everything a blade has to offer without compromising the safety of a blade by cutting corners to bring out its activities.
This is not a tutorial or a DIY walkthrough of how to polish. This is just a quick overview of how I polish. Over the years, I’ve seen and heard people become “Professional or Traditional Polishers” overnight after reading some books, websites, buying some stones, or even going to a sword shows talking to people. There is a lot more involved in polishing than what I’m going to explain here. Traditional Japanese Sword polishing is a very meticulous and tedious process that requires skill, patience, knowledge, control and so on. If you’re really interested in learning this craft, find a teacher that will work with you in person. If you have a sword that needs to be polished, make sure that you’re sending it to a reputable polisher that will not harm your sword.
Shitaji – Foundation Polish – Ground Work
Shitaji is the *most* important thing when polishing a Japanese Blade. It is critical that the foundation polish of a blade is done properly from the start to obtain a good overall polish. Some people may think that polishing is a process of removing scratches until the hamon on a blade is visible. This is not so. There’s a lot more to traditional polishing than bringing out the activities of a blade. Regardless of what blade I’m working on or have worked on, or how much a particular smith had prepared the blade for polishing, adjustments are still necessary in order to get the full potential of the finished product. Setting the geometry and symmetry of the blade, checking and/or fixing niku, wobbles on the surface, crispness of the shinogi-ji and mune, etc are standard fare. Whether it be subtle or drastic adjustments, every single blade that I’ve worked on has been tweaked in some way to correct its geometry, symmetry etc. This is done while maintaining the smiths vision of the blade in full polish.
I use a series of Japanese polishing stones that I get directly from Japan. The stones are available in either synthetic or natural form. Over the years I’ve acquired collection of each stone and learned which one will work best on a particular blade that I’m working on i.e. Nihonto or Modern Day steel blades.
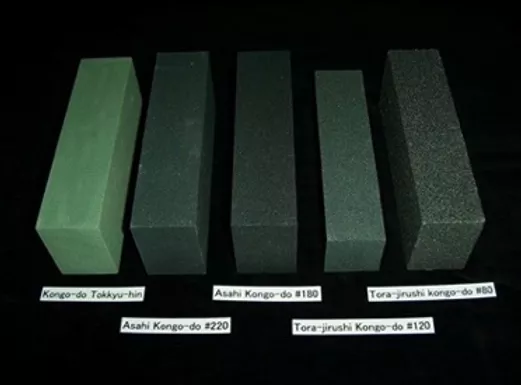
Kongo-do
This is usually used to set or make drastic adjustments to a blade’s geometry. It removes heavy rust pits and chips on a blade. This stone is very aggressive and could easily ruin a blade if used improperly. I rarely use this stone since most of the blades that I acquire are new, and most arrive in binsui-do finish. I’ve never polished a blade that came straight out of the heat treat in a condition that necessitates that I set the edge, niku, etc. of the blade. I’m working my way up to that level still but I would like to perfect where I am right now before I move on to the next level.

Binsui-do
I use this stone primarily to define/tweak a blade’s geometry. This is one of the stones that I will spend a lot of time with to set a blade’s geometry and give it ample definition. As a plus, it also refines the scratches of the previous stone (Kongo-do).
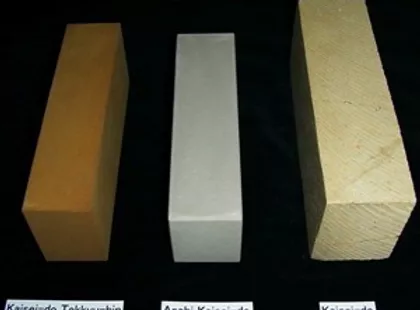
Kaisei-do
This stone is used to remove the scratches of the Binsui-do stone. This is also the final stone for setting and defining the geometry. While using this foundation stone, it is a *must* that the blade’s geometry is constantly checked to make sure that all the lines are kept straight, symmetrical and sharp. One wrong stroke can remove too much material, gouge the blade, and may create new wobbles and various other mishaps that could very easily destroy a blade. Each stone’s purpose is to redefine the result of the previous stone.
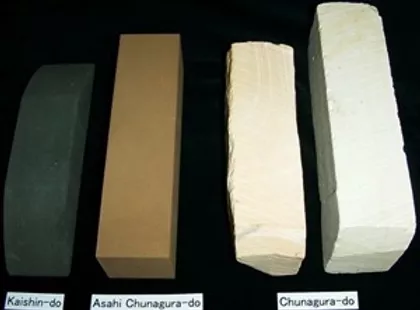
Chunagura-do
This stone is used to remove the Kaisai-do scratches. From this stone on, its basically scratch removal although the geometry of the blade is always maintained and checked. I can’t stress this enough because if a blade’s geometry is incorrect, then it doesn’t matter how the activities are brought out. In the end, the blade will still look haphazardly polished.
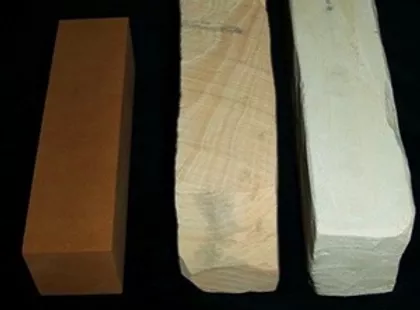
Komanagura-do
This stone is very soft and fine. It is used to remove/refine the scratches of the Chunagura stone and prepares the blade for Uchigumori Stage.
Kaishin-do
This stone could be used as a substitute to the nagura stones in groundwork. Again it depends on the blade that I’m working on.
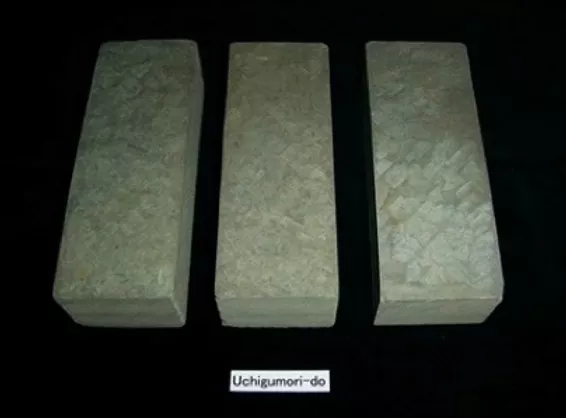
Uchigumori Hado
This is a very fine and soft stone that is used on the Ha (hardened edge) to define the hamon and bring out any hararaki on the yakiba.
Uchigumori Jido
This is a much finer and usually a little harder stone stone than the Hado. Jido is used to bring out the Jihada (grain pattern) of the blade.
The use of these last two stones are the most difficult to master. These stones are only available in natural form and often cost a lot. It takes a lot of patience and skill to use these stones properly. They could scratch a blade easily and could ruin many hours of work in the foundation polish. This is because a blade needs to be taken back down again after a serious scratch from this stone. Since I have to match the stone to the blade I’m working on, I have to be able to pick out an uchigumori stone with the hardness that will work best. It is best to have a good collection of all the necessary stones in order to find the right one that will work on a particular blade. That collection could get very expensive.
Shiage – Finishing Polish
Tsuya (finger stone work) – This is the process where I will take a piece of uchigumori stone backed with tanned yoshino-gami lacquered and sized to fit underneath my thumb. The stone is thinned to a paper thin width and rubbed on the blade with tojiru (polishing paste made by rubbing 2 uchigumori stones together).

Hazuya
These are thinned pieces from uchigumori koppa. It is used to polish the yakiba (hardened edge) of the blade. This will give the yakiba a more white and milky look and helps make the habuchi stand out.

Jizuya
These are thinned pieces of narutaki koppa. This stone is used on the Ji of the blade to define the blade’s jihada, if any. I use this stone in two ways. The blade I’m working on will determine if I need to use both steps.
Konashi
This entails using a piece of jizuya along with some tojiru, and using it only on the Ji surface of the blade.
Metoshi
This entails using a piece of jizuya (backed or not backed) that is broken into little pieces, and constantly washing away any residue with clean water.
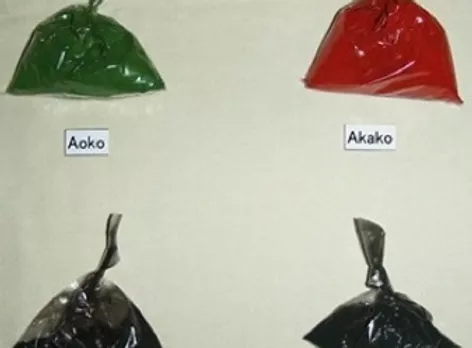
Nugui
This is the final process of making everything stand out on the blade. Specifically the hamon, jihada and any other hataraki that is present on the blade. Since I tend to favor the sashikomi style of polish, proper nugui mixture could make a big difference in the blade’s final look. I use jitekko, aoko, uchiko, akako, etc. or a combination of powders to make my nugui. Again it will depend on the blade that I’m working on and how much contrast I want to get out of the blade. I’ve experimented a lot of times using different nugui recipes that will work well with any blade. This is the point where I decide if I should finish the blade using a traditional method or using a traditional/hybrid method. I find a traditional/hybrid method works better with blades made with modern day steel for a more traditional look. Some steels don’t like nugui very much; it does not react properly with nugui because of its vanadium and carbide content. This is also where I would use a traditional/ hybrid polish to get the most I can out of the blade that I’m working on.
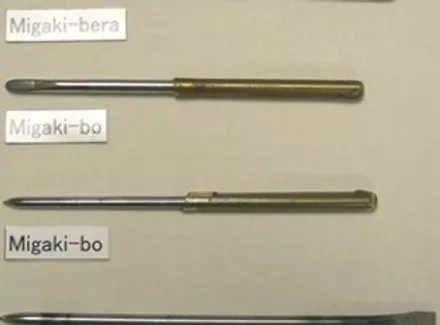
Migaki-Togi
(Burnishing the Shinogiji and the Mune) – is the process of burnishing the blades shinogiji and mune to a high mirror shine. I use three different kinds of burnishing rods in 2 stages, namely Shitamigaki (Foundation Burnishing) and Uemegaki (finishing Burnishing). Ibota powder is used so that my migakibo will slide on top of the steel and burnish the surface to a mirror shine.
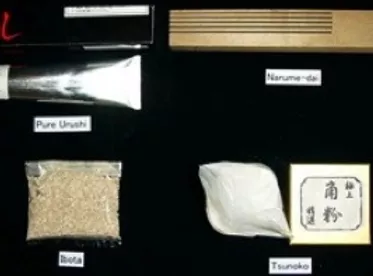
Sugikiri
(Defining the Yokote). This is the process where I would use a piece of hazuya to polish out the tip on a shinogi zukuri blade at a 90-degree angle. This gives the kissaki more of a whitish look than the rest of the blade. This process also brings out the boshi.
Narume
Polishing of the Hakissaki. A bigger piece of thinned hazuya on top of narume-dai is used on this stage. This is the stage that takes the ha-kissaki to a scratch free finish. This is the last stage of my polishing.
Nagashi
Polisher’s Signature. Most polishers in Japan will put their nagashi on a blade upon completion signifying the school. The lines appear as a series of 7 to 13 lines underneath the habaki on the shinogiji. Sometimes there are also 3 lines on each side of the mune towards the tip area of the blade.